top of page
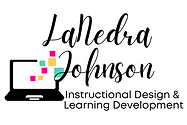.png)
Getting Started In Metal Stamping

Analysis of Project
Challenge:
Parts are not being run properly, by new employees, which has been resulting in customers being dissatisfied with the finished product and returning them to the lab. Over the last two years, this has cost the company approximately $50,000 in lost parts. The company owner and the Product Manager wanted to determine what was the cause. After speaking, it was determined that there was a high new employee turnover rate and that new employees were being put into the Production Lab prematurely. Ultimately, new employees were not fully aware of all the job entailed and had not received background and hands-on training prior to beginning in their new role.
Project Overview:
This project is important because it was designed to provide new production employees with the adequate skills needed to produce quality parts in a timely manner with the overall goal to reduce the cost of manufacturing operations.
The organization's overall business goal is to show a loss of reduction of at least 98% by improving quality. This project is important because, if successful, it will result in an increase of customer renewals by at least 15%, when compared to overall new client renewal rates.
The overall instructional goal for this project was to educate new members of the production team so that they could learn how to get started and know the basic fundamentals of using the company's equipment.
Audience & Prerequisites:
-
New employees to the Production Lab
-
18 - 55 years old
-
Capable of lifting up to 70 lbs
-
Ability to withstand extreme heat
-
Able to stand for long periods of time
-
Ability to come up with solutions in stressful situations
-
Able to read blueprints and use a basic measuring device
Design & Developent of Project
Curriculum Design:
After speaking with the SME and based on the training needs, I determined that an in-person training with a hands-on component would be necessary. This ILT would include slide decks, a trainer guide, a participant guide, and a job aid that would explain the process of working in production and provides a step-by-step framework of the machines and the parts used while on the job.
Assessment:
We will know that the training is successful when new employees are able to:
-
Power on the machine including the hydraulic and auxiliary pumps
-
Read a shop traveler and select the correct tools from the rack
-
Use set-up sheets to set up and program the dies to run properly
-
Run sample parts and have them approved by the Quality Lab
​
Deliverables:
-
Slide Deck
-
Infographic Job Aid
-
Trainer Manual
-
Participant Guide
-
Training Evaluation Form
-
Performance Assessment Checklist
​
Tool Used:
-
Canva Pro
View Slide Deck
Trainer Guide
Learner Guide
Infographic Job Aid
Implementation of Project
New Employees (learners) will receive the training live inside of the shop by a trained employee of the company. There is no need for a Train the Trainer, as the person selected to facilitate the training is familiar with how the company runs. To ensure that the training is a success, new employees will have time to practice working through each step with the guidance of a mentor.
Evaluation of Project
After the training, trainees will complete an Evaluation Form to provide their insight on the training they received and how it helped to prepare them for success in their new position.
For a more concise determination of the success of the training, trainees will also participate in a performance-based assessment to demonstrate their ability to perform the tasks detailed in the learning objectives.
During the performance-based assessment, the Product Manager will verbally assign the trainee a tool to produce. The trainee will:
1. Use the Shop Traveler and Tool Sheet to select
2. Power on the machine (main power, auxiliary, and hydraulic)
3. Set up the dies
4. Refer to the setup sheet to program the dies
5. Load materials and run the parts
6. Have parts approved by Quality Lab
It will be evident that the training was successful when more quality parts are being produced as evidenced by a reduced percentage of parts being lost and an increase in customer satisfaction as evidenced by more renewals for work.
Performance Assessment Checklist
Evaluation Form
bottom of page